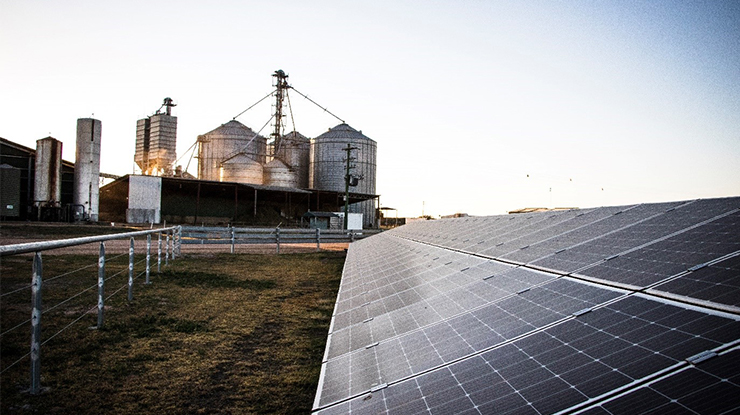
Teys targets energy usage
Key points
- Teys Australia Condamine Feedlot is hosting a research project investigating solutions to reduce energy usage and the environmental footprint of Australian feedlots.
- A Utility Management System has been installed across the site to monitor and measure water, gas and electricity usage in real-time.
- Six months into the 12-month project, measurements have shown thermal energy accounted for 86% of total energy usage.
Finding solutions to reduce energy usage and the environmental footprint of Australian feedlots is the focus of a research project now underway at Teys Australia Condamine Feedlot.
The 30,000-head feedlot in Queensland’s Western Downs region is hosting the project, which has seen a Utility Management System installed across the site to monitor and measure water, gas, and electricity usage in real-time.
Smart Business Hub Director, Carl Duncan, is leading the 12-month project, funded by MLA in consultation with the Australian Lot Feeders’ Association (ALFA).
Next-level innovations
Carl said the feedlot had already reduced energy costs by 40% and utility related greenhouse gas emissions by 50% before the project started, making it the ideal site to explore next-level innovations in energy and water management systems.
“We cherry-picked strategic locations in the field for the energy meters, and we have an IT system that sends data from the meters to the cloud and into a software package that enables us run analytics to identify opportunities in real-time operations,” Carl said.
“By having transparency over energy use in real-time with customised dashboards and alerting, it will identify opportunities to save energy and reduce the environmental footprint.”
Targeting thermal energy
Six months in to the 12-month project, measurements have shown thermal energy accounted for 86% of total energy usage.
“To monitor thermal energy, we’ve metered off fuel input going into the boiler and steam outputs so we can measure the efficiency of the thermal system, and that’s key because it’s usually the biggest area of opportunity in a feedlot where gains can be made,” Carl said.
“Looking at water, the project is monitoring how much water the cattle are drinking; how much is evaporating from the turkey’s nest; how much is used for dust suppression and process water for the flaking plant and boiler.
“And for electricity, we’ve metered off things like the mill plant and each of the mill plant motors, the tub grinder, batching facility, workshops, and compressed air stations.
“Feedlots are often at fringe of grid locations where energy costs per unit are high – having the right tools to better manage this business input cost is key.”
Reducing reliance on electricity
Teys Australia Condamine Feedlot General Manager, Phil Lambert, said over the past four years the feedlot had implemented a range of measures including installing at 300-kilowatt solar system to mitigate energy usage.
“We put a lot of effort into reducing our reliance on electricity particularly, and we’ve made some changes around gas and thermal heating. However, we really wanted to drill down further into the data to look at other opportunities to reduce energy use,” Phil said.
“The mill is our major energy user for gas for the boilers for steam for milling our grain and it’s also our largest user of electricity, with at least 80% of our electricity usage coming from that area.
“Since the project has been underway, it has definitely highlighted opportunities for further efficiencies with the boilers to create steam for milling.
“If there has been a major change in the baseline, the system has obviously alerted us to that, so we can pick up an issue before there’s a spike in energy use and determine its cause."
“We plan to continue to use these meters after the project has finished so we can use data to improve efficiencies in operations, whether that be benchmarking the energy costs associated with different grains, or the efficiency of particular operators.”
The project is set to finish by November 2020 and its findings are due to be released by January 2021.